Lubrication-cooling and metalworking: an integrated system
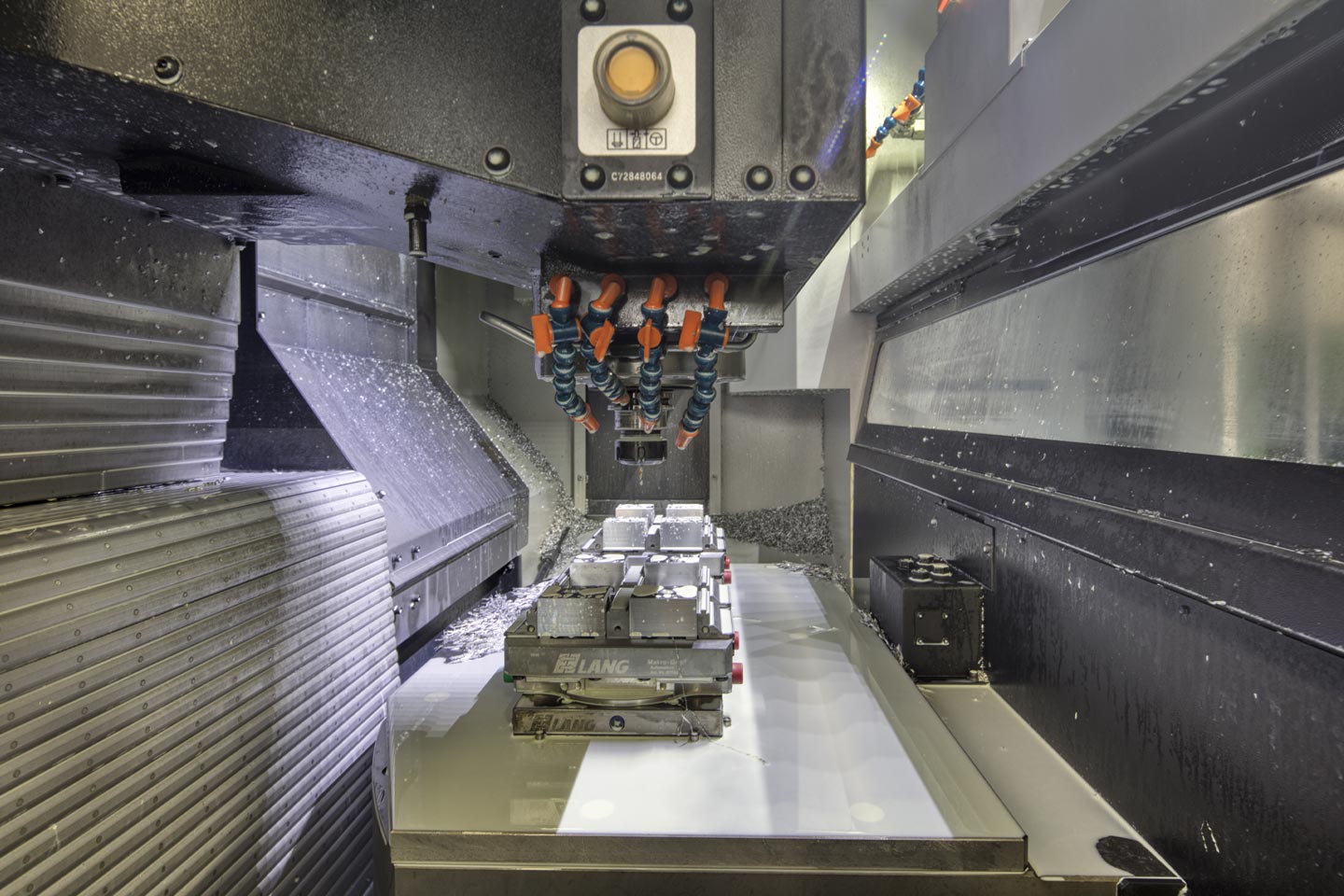
In metalworking, the chip removal that occurs during turning, milling, grinding, and grinding operations requires the use of cooling lubricant fluids (FLRs) also called cutting oils or metalworking fluids. Such fluids essentially serve two purposes: to cool the machining area, which is subject to overheating due to continuous and severe mechanical stresses; and to optimally lubricate the tool-workpiece contact, to reduce friction and dissipate the heat produced-which can even exceed 1000°.
It therefore seems evident how much and how lubrication-coolant has a direct influence not only on the quality of machining, but also on the life and performance of the machine tool, so much so that it is now considered an integral part of it. In fact, an efficient lubricant makes it possible to work in optimal conditions: it has been estimated that, annually, production downtime related to inadequate systems negatively affects overall company productivity (minus 10 percent).
In order to avoid problems and limit maintenance work on machinery as much as possible, it is absolutely necessary that the cutting fluid-relative to its composition in terms of additives-be appropriate to the type of machining and the nature of the metals used in production. Commercially, there are essentially two types: whole FLRs (which contain no water) and soluble FLRs (to which water is added in varying proportions). The main characteristics to evaluate when choosing the right fluid for your needs are: stability, detergency, shear potential, decay range, and versatility. On the other hand, there are two variables to watch out for.
The first concerns cleanliness, which must be ensured by means of an appropriate filtration system to prevent chips and metal dust from machining or thermal degradation from getting into the fluid. Adequate filtration also serves to avert the danger of biological contamination, by microorganisms (bacteria and fungal species) that, by spreading into the environment in the form of bioaerosols, can cause respiratory and dermatological diseases.
The second variable, however, relates to sustainability. In the last decade-thanks mainly to the efforts of major manufacturers and distributors-there has been a trend toward the increasing use of renewable-based coolants (with vegetable esters instead of hydrocarbons), which pollute less and can be more easily disposed of. Like all process chemicals, lubrorefrigerants are also monitored by the relevant legislation: the REACH (European Regulation concerning the Registration, Evaluation, Authorization and Restriction of Chemicals), which requires the ECHA European Chemical Agency to periodically update the Candidate List, the list of carcinogenic, mutagenic and toxic substances(SVHC substances). Safety Data Sheets (SDSs), which by law must accompany metalworking oils and industrial lubricants, contain all the information essential for proper and judicious use of the product.
The law also establishes procedures to be followed in disposal operations-as FLRs are considered, like most technical fluids, as special waste. In Italy, CONOU Consorzio Nazionale degli Oli Minerali Usati, introduced in 1982 by Presidential Decree, is the first environmental agency dedicated to the collection, management and transformation of used oils from waste to resources. As confirmed by the latest sustainability report released by the organization, The Consortium can be considered a model at the forefront in the international field: while in Europe a share of 60 percent of the used lubricating oil collected is sent to regeneration, in Italy this ratio reaches about 99 percent, and the process is capable of guaranteeing several benefits such as, among all, the reduction of fossil fuel consumption for the production sector and, as a consequence, the reduction of CO2 emissions into the atmosphere.
Compliance with industry regulations, in addition to being the only possible guarantee for safeguarding the health of workers, is therefore a valuable control tool for companies and metalworking shops that intend to operate in compliance, guarantee the highest quality of their manufactured goods and translate the impact of a virtuous system into marginality. Like Piacenza Meccanica, which, through a structured program of investments in technologies, processes and safety, translates its values into competitive advantage.