Lubrorefrigerazione e lavorazione dei metalli: un sistema integrato
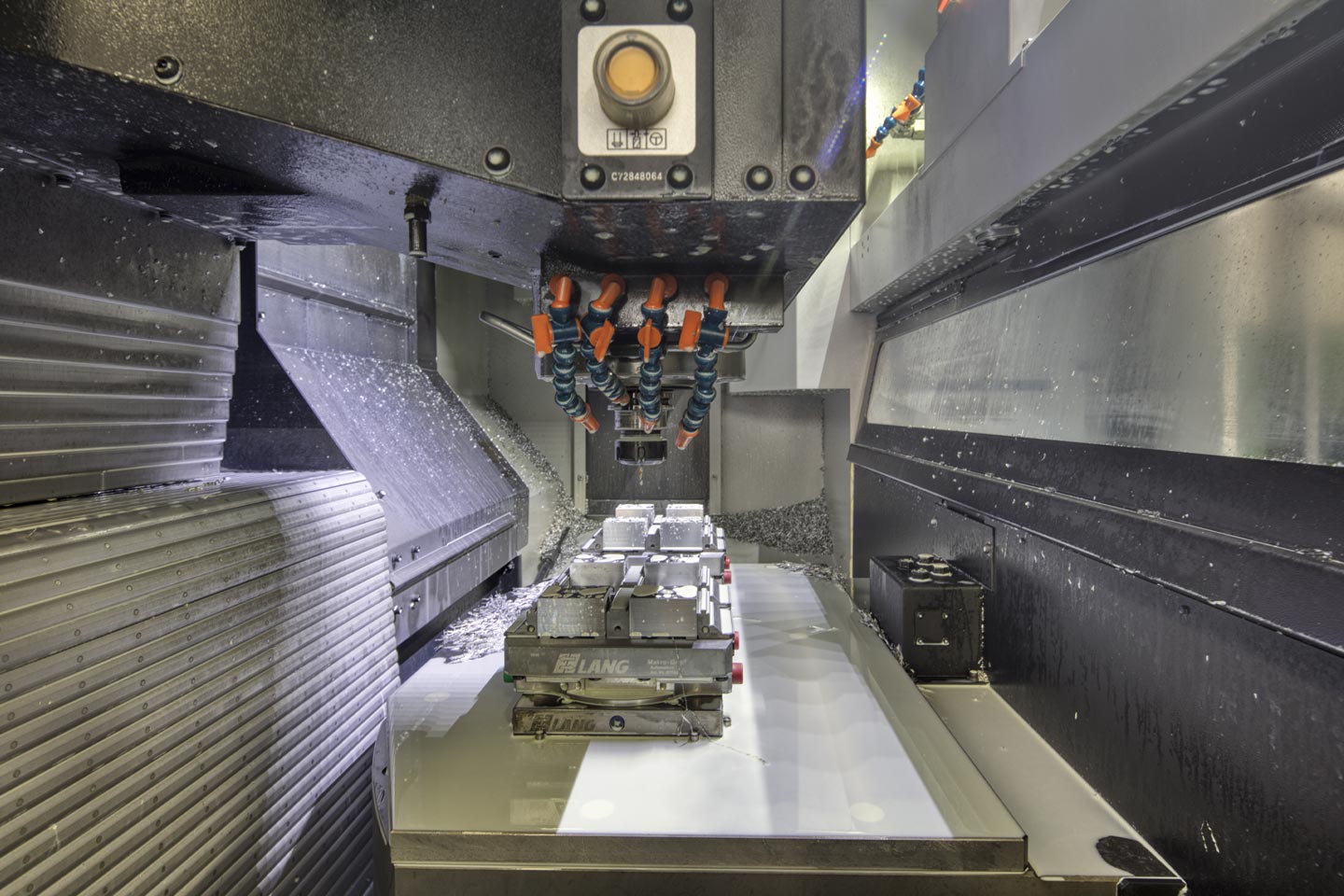
Nelle lavorazioni metalmeccaniche, l’asportazione di truciolo che si verifica durante le operazioni di tornitura, fresatura, molatura e rettifica richiede l’uso di fluidi lubrorefrigeranti (FLR) detti anche oli da taglio o metalworking fluids. Tali fluidi hanno essenzialmente un duplice scopo: raffreddare la zona di lavorazione, soggetta a surriscaldamento a causa delle continue e severe sollecitazioni meccaniche; lubrificare in modo ottimale il contatto utensile-pezzo, per ridurre l’attrito e dissipare il calore prodotto – che può persino superare i 1000°.
Appare dunque evidente quanto e come la lubrorefrigerazione abbia un’influenza diretta non solo sulla qualità delle lavorazioni, ma anche sulla vita e sulle prestazioni della macchina utensile, tanto da esserne ormai considerata parte integrante. Un lubrificante efficiente permette infatti di lavorare in condizioni ottimali: è stato stimato che, annualmente, i fermi di produzione correlati a sistemi inadeguati, incidono negativamente sulla produttività aziendale complessiva (meno 10%).
Per evitare problemi e limitare al massimo gli interventi di manutenzione sui macchinari, è assolutamente necessario che il fluido da taglio – relativamente alla sua composizione in termini di additivi – sia appropriato alla tipologia di lavorazione e alla natura dei metalli impiegati nella produzione. In commercio, ne esistono essenzialmente due tipi: FLR interi (che non contengono acqua) e FLR solubili (cui viene aggiunta acqua in proporzione variabile). Le principali caratteristiche da valutare nella scelta del fluido adatto alle proprie esigenze sono: stabilità, detergenza, potenziale di taglio, intervallo di decadenza, versatilità. Le variabili da tenere sotto controllo sono invece due.
La prima riguarda la pulizia, che deve essere garantita mediante un opportuno sistema di filtrazione per impedire che nel fluido finiscano trucioli e polveri metalliche derivanti dalle lavorazioni o dalla degradazione termica. Una filtrazione adeguata serve inoltre a scongiurare il pericolo di contaminazione biologica, da parte di microorganismi (batteri e specie fungine) che, diffondendosi nell’ambiente sotto forma di bioaerosol, possono provocare patologie respiratorie e dermatologiche.
La seconda variabile è invece relativa alla sostenibilità. Nell’ultimo decennio – grazie soprattutto all’impegno dei principali produttori e distributori – si registra la tendenza ad un impiego sempre più massivo dei lubrorefrigeranti a base rinnovabile (con esteri vegetali al posto degli idrocarburi), che inquinano meno e possono essere più facilmente smaltiti. Come tutti i prodotti chimici di processo, anche i lubrorefrigeranti sono attenzionati dalla normativa di riferimento: la REACH (Regolamento Europeo concernente la registrazione, la valutazione, l’autorizzazione e la restrizione delle sostanze chimiche) che prevede l’aggiornamento periodico, da parte della ECHA European Chemical Agency della Candidate List, l’elenco delle sostanze cancerogene, mutagene e tossiche (SVHC substances). Le Schede Dati di Sicurezza (SDS), che per legge devono accompagnare oli per metalworking e lubrorefrigeranti industriali, contengono tutte le informazioni indispensabili ad un uso corretto e oculato del prodotto.
La legge stabilisce inoltre le procedure da seguire nelle operazioni di smaltimento – essendo i FLR considerati, al pari della maggior parte dei fluidi tecnici, come rifiuti speciali. In Italia, Il CONOU Consorzio Nazionale degli Oli Minerali Usati, introdotto nel 1982 con decreto del Presidente della Repubblica, è la prima agenzia ambientale dedicata alla raccolta, alla gestione e alla trasformazione degli oli usati da rifiuti a risorse. Come conferma l’ultimo rapporto di sostenibilità rilasciato dall’organizzazione, Il Consorzio può essere considerato un modello all’avanguardia in campo internazionale: mentre in Europa si avvia a rigenerazione una quota pari al 60% dell’olio lubrificante usato raccolto, in Italia questo rapporto arriva a circa il 99% e il processo è capace di garantire diversi benefici quali, tra tutti, la riduzione del consumo di combustile fossile per il comparto produttivo e, in conseguenza, l’abbattimento delle emissioni di CO2 in atmosfera.
Il rispetto della normativa di settore, oltre ad essere l’unica garanzia possibile per la salvaguardia della salute dei lavoratori, risulta dunque essere un prezioso strumento di controllo per aziende e officine metalmeccaniche che intendono operare in conformità, garantire la massima qualità dei propri manufatti e tradurre in marginalità l’impatto di un sistema virtuoso. Come Piacenza Meccanica che, attraverso un programma strutturato di investimenti in tecnologie, processi e sicurezza, traduce i propri valori in vantaggio competitivo.