Produzioni metalmeccaniche al servizio dell’industria ferroviaria: una storia lunga un secolo
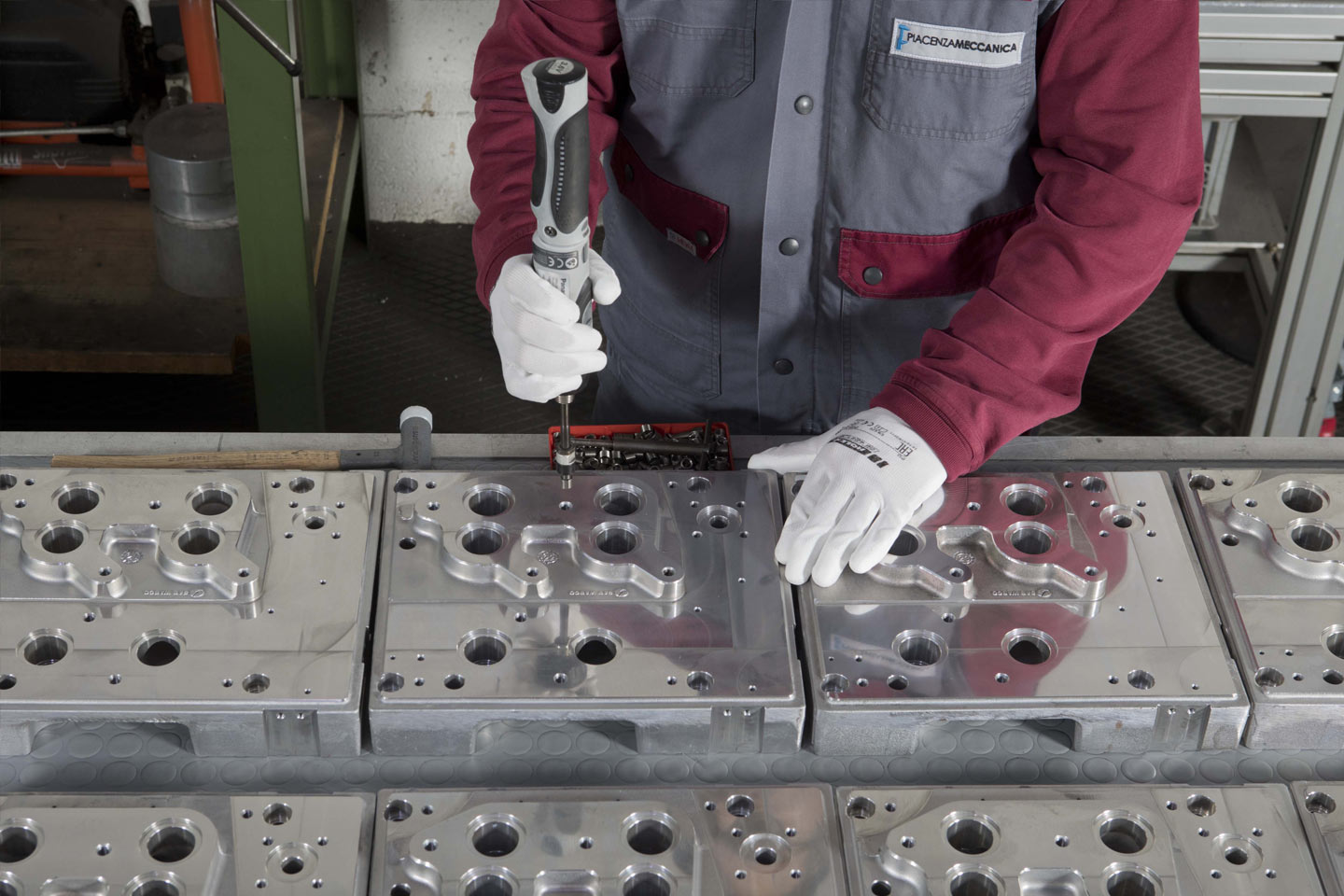
Nell’aprile del 1869, a soli ventitré anni, George Westinghouse riuscì a convincere funzionari ed esperti dell’infrastruttura ferroviaria locale a testare il prototipo del suo nuovo sistema di frenatura per treni. Montato su un convoglio composto da una locomotiva e 4 vagoni, partito dalla stazione di Pittsburgh, l’impianto frenante ad aria compressa rivelò la sua efficacia quando il mezzo, lanciato alla velocità di 50 km/h, riuscì a fermarsi poco prima dell’impatto con un carro agricolo, accidentalmente fermo sui binari.
Nonostante la performance il giovane non era soddisfatto della propria invenzione e, nei tre anni a seguire, continuò a lavorare al suo perfezionamento; fin quando riuscì a ridurre tempi e spazi di frenata e a risolvere la principale vulnerabilità del sistema – ovvero l’assenza di un meccanismo in grado di garantire l’arresto del treno anche in caso di parziale avaria dell’impianto frenante. Fu grazie all’introduzione di un ulteriore componente metalmeccanico – la valvola tripla o distributore – che il freno pneumatico raggiunse la massima affidabilità e, ancora oggi, la tipologia di impianto che regola la frenatura o la sfrenatura della maggior parte dei rotabili in circolazione,resta quello ideato dal giovane newyorkese oltre un secolo fa.
Il freno continuo automatico Westinghouse: un capolavoro di ingegneria e meccanica
Da est a ovest, il freno continuo automatico Westinghouse o FCA è lo standard di riferimentoper la maggior parte dei sistemi frenanti ferroviari mondiali. In questa tipologia di impianto, tutti ivagoni sono collegati pneumaticamente tra loro mediante la condotta generale o condotta del freno. La caduta di pressione, regolata dal comando di freno o rubinetto di comando posto in cabina di guida e azionato dal macchinista, propagandosi lungo tutto il treno, raggiunge le varie apparecchiature frenanti del convoglio, e aziona pistoni e cilindri dei freni.
Il processo è semplice e sofisticato allo stesso tempo. L’aria necessaria ad alimentare il sistema viene prelevata dall’esterno e spinta, attraverso un filtro di pescaggio che cattura le impurità grossolane, verso uno o più compressori. La massa d’aria pressurizzata a 8-10 bar viene poi nuovamente filtrata ed essiccata tramite assorbimento (ovvero per azione di sostanze chimiche in grado di trattenere il vapore acqueo); infine, viene immagazzinata nel serbatoio principale cheaccoglie e stocca i volumi d’aria necessari ad alimentare l’impianto frenante e gli impianti di servizio del treno (ad esempio il meccanismo di apertura e chiusura porte). Quando il macchinista aziona il comando del freno, abilita il passaggio di aria compressa alla pressione di 5 bar dal serbatoio principale lungo la condotta generale. La variazione dei valori pressori sollecita il distributore che intercetta il passaggio dell’aria, confronta i valori di pressione della condotta generale e del serbatoio di comando connesso al freno, e converte l’informazione in bar in impulso da trasmettere al cilindro.
Il distributore o valvola tripla, è dunque a tutti gli effetti un componente chiave dell’impianto frenante in quanto mette in comunicazione gli elementi del sistema che realizzano la frenatura e provocano la sfrenatura, quando l’aria esce dal cilindro freno e viene nuovamente liberata in atmosfera. Il funzionamento di questo sistema chiuso – e di conseguenza la sicurezza di merci e passeggeri in viaggio – è garantito dall’affidabilità e dalle performance di tutte le parti che compongono l’insieme.
Piacenzameccanica sui binari della storia
Storicamente, il sistema ferroviario europeo è stato gestito su base nazionale dai singoli stati membri tramite apposite aziende monopolio, spesso alle dipendenze dei relativi Ministeri, incaricate di occuparsi de: la predisposizione dell’infrastruttura e del materiale rotabile; la regolamentazione del servizio; la sicurezza. La direttiva CEE 440/1991 ha imposto la prima separazione tra la gestione dell’infrastruttura e quella dei servizi di trasporto; e altre norme emanate negli anni a seguire hanno contribuito alla liberalizzazione definitiva del sistema ferroviario per cui oggi vige un sistema ibrido, che vede più interlocutori coinvolti nella stessa mission.
In Italia, RFI Ferrovie dello Stato Italiane gestisce l’infrastruttura nazionale secondo i metodi e i criteri stabiliti dalla Direttiva UE 798/2016. Per effetto di tale norma, le industrie che si occupano della produzione e della fornitura dei mezzi rotabili sono i medesimi soggetti incaricati e responsabili delle operazioni di manutenzione periodiche sugli stessi. Del glorioso passato industriale che vide il nostro paese sul podio delle nazioni che si distinsero nella produzione di materiale rotabile ferroviario, non resta un granché e gli attori rimasti in scena, ad oggi, sono pochi: i giapponesi Hitachi Rail che, dopo l’acquisizione della Ansaldo Breda nel 2015, rifornisce di mezzi i principali operatori italiani; i tedeschi Knorr-Bremse o gli american Wabtec Corporation, entrambi leader nella produzione di sistemi frenanti.
Si tratta per lo più di multinazionali e grandi gruppi industriali che hanno seguito un percorso di evoluzione e crescita parallelo al settore ferroviario, per poi distinguersi in termini di competenze, know-how e qualità di prodotto ed affermarsi come oligopolio. Da tre generazioni ed ancora oggi, Piacenzameccanica interagisce con i giganti che producono i migliori sistemi frenanti al mondo,rifornendoli di componenti metalmeccanici di altissima precisione. Dalla valvola tripla che è il cuore dell’impianto, alla valvola di scarico che evita il sovraccarico del sistema; dai rubinetti di intercettazione che uniscono pneumaticamente i vari convogli consentendo la continuità della frenata, al rubinetto di isolamento per escludere dal freno, in caso di guasto, le apparecchiature frenanti.
Anche in uno scenario dinamico e orientato all’avanguardia come quello del settore ferroviario che deve gestire volumi di utenza e velocità sempre più importanti, è paradossale quanto stranamente rassicurante constatare come anche i sistemi più innovativi e complessi, per funzionare, abbiano bisogno di tecnologie e competenze eterne, ad oggi riadattate secondo le linee guida BAT e tradotte in processi 4.0 – come nel caso delle lavorazioni metalmeccaniche di precisione per il settore ferroviario firmate Piacenzameccanica.