Precision mechanics: ideal tools for every machining operation
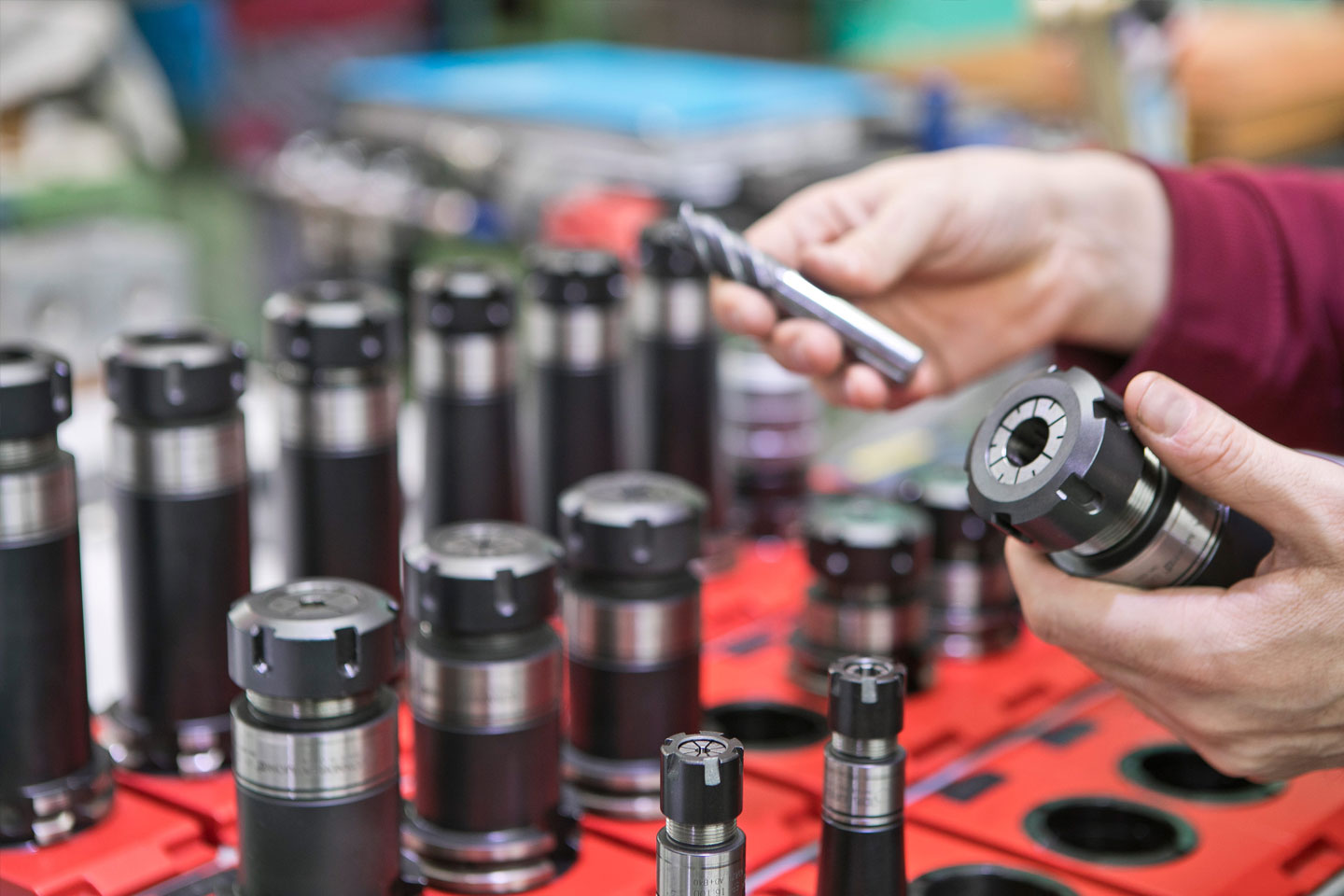
In precision machining, there is a foundational and fundamental rule-a mantra that inspires shop floor work, conditions investment policies and business positioning strategies: minimize errors.
The variables on which it is possible to intervene to achieve the best result and reduce the incidence of defective components in the total volume, affect both the design and production phases and concern, essentially, the expression of particularly tight tolerances and the use of technologies designed for the purpose of increasing productivity and reducing production waste.
Going into detail about the most effective systems in terms of business profitability, at the first point we find CNC machining centers that should be able to offer performance and competitiveness in all their performance. Solutions that autonomously manage machine tooling and tool change, allowing smooth and fast transitions from one machining operation to another, are those that arouse the most interest among those in the industry.
Multi-pallet machines for example-which we have already devoted an in-depth article to on our blog-allow almost simultaneous operation on different processes, allowing finished and semi-finished parts to be alternated without having to stop the machine.
Pallet changing systems, whether manual or automated, achieve maximum efficiency with zero-point clamping, which allows the workpiece to be quickly clamped and clamped, eliminating the need for complex measurements and adjustments each time machining changes.
The choice of the most suitable system for one's company depends on the type of customer requirements and, consequently, on production needs; however, there are a number of features that would be worth considering beforehand in order to evaluate the return on any investment. We are not just talking about the precision and tightness of anchoring by means of clamps, jaws, mechanical or pneumatic grips. For a clamping system to be truly valuable, it must be: versatile, meaning compatible and adaptable on different machine tools; expandable, to be able to handle parts of varying sizes and geometries; and modular, to be able to work at different heights.
To navigate the choice in short, one must first evaluate all possible applications and clamping situations that the system might face. Positioned inside CNC milling machines and lathes, the zero point is the pivot around which the machine's tools move and work. The more you aspire to special machining with holes, pockets, slots, and irregular contours, the greater the need forwell-rounded tooling.
Depending on the machining to be done, different types of cutters are needed - helical, staggered-tooth, double-angled, flat, candle, chamfering, face - and turning tools - roughers, finishers, cutters or threaders. For drilling, depending on the diameter and finish of the hole, drills with special geometries are required - integral, insert, keeper, cannon - possibly equipped in turn with internal holes for the adduction of coolants. With the aim of satisfying even the most particular requests, PiacenzaMeccanica has for years pursued a structured policy of investment to cut production times and improve the quality of its products; not only through state-of-the-art machinery, but also by implementing its own collection of tools.