Meccanica di precisione: strumenti ideali per ogni lavorazione
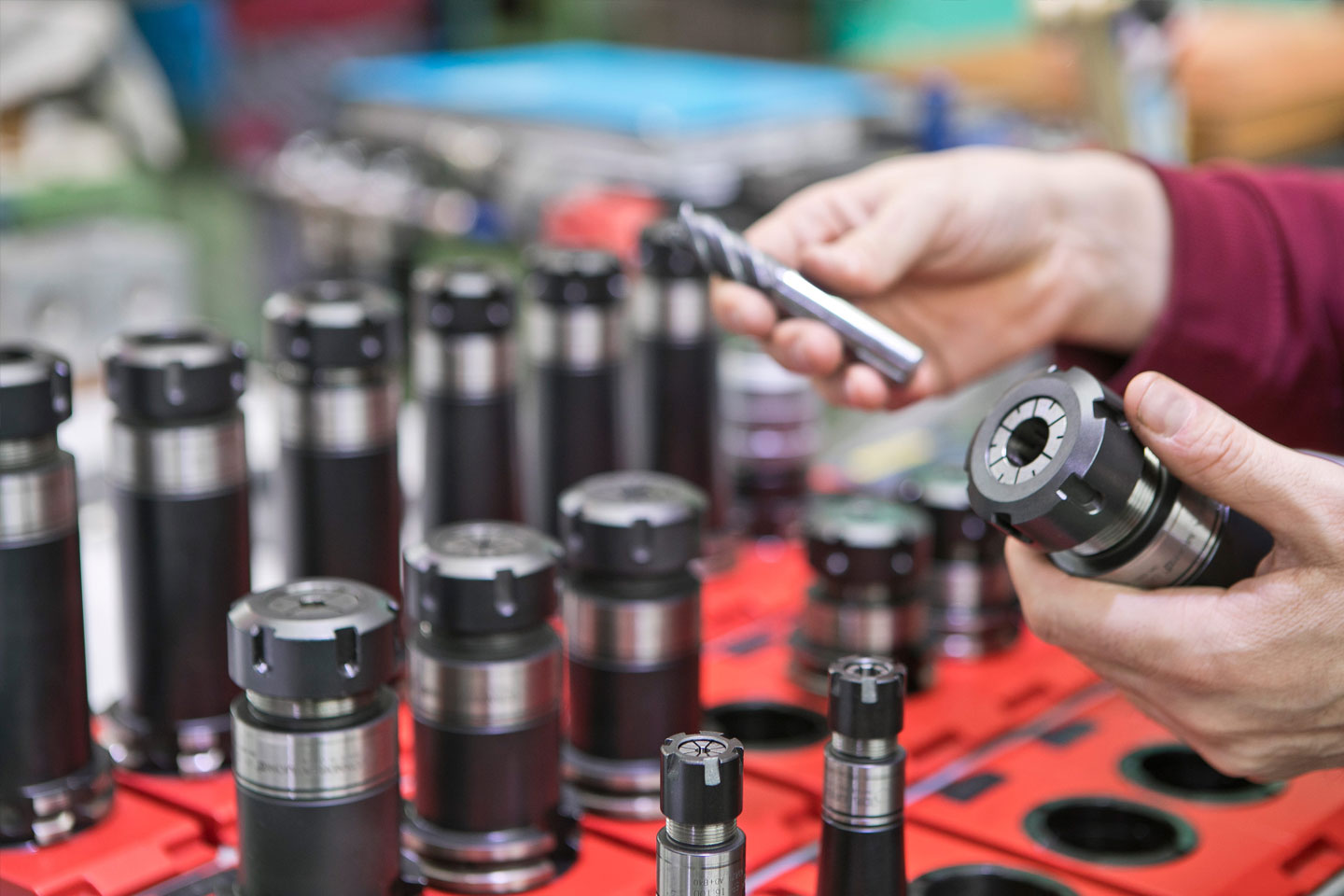
Nell’ambito delle lavorazioni meccaniche di precisione, c’è una regola fondante e fondamentale – un mantra che ispira il lavoro in officina, condiziona le politiche di investimento e le strategie di posizionamento aziendale: minimizzare gli errori.
Le variabili sulle quali è possibile intervenire per ottenere il miglior risultato e ridurre l’incidenza di componenti difettati sul totale del volume, interessano sia la fase progettuale che quella produttiva e riguardano, sostanzialmente, l’espressione di tolleranze particolarmente strette e il ricorso a tecnologie progettate allo scopo di aumentare la produttività e ridurre gli scarti di produzione.
Scendendo nel dettaglio dei sistemi più efficaci in termini di redditività di impresa, al primo punto troviamo i centri di lavoro CNC che dovrebbero essere in grado di offrire performance e competitività in ogni loro prestazione. Le soluzioni che gestiscono in autonomia l’attrezzaggio della macchina e il cambio utensili consentendo transizioni fluide e veloci da una lavorazione all’altra, sono quelle che destano maggiore interesse tra gli addetti ai lavori.
I macchinari multipallet ad esempio – cui abbiamo già dedicato un approfondimento sul nostro blog – consentono di operare in maniera pressoché simultanea su differenti lavorazioni, permettendo di alternare i pezzi finiti con quelli semilavorati senza dover fermare la macchina.
I sistemi a cambio pallet, sia esso manuale o automatizzato, raggiungono il massimo della loro efficienza grazie al serraggio a punto zero che consente di fissare e bloccare rapidamente il pezzo da lavorare, eliminando la necessità di misurazioni e regolazioni complesse ogni volta che cambia la lavorazione.
La scelta del sistema più adatto alla propria azienda dipende dalla tipologia delle richieste dei clienti e, di conseguenza, dalle esigenze di produzione; ci sono tuttavia una serie di caratteristiche che sarebbe opportuno tenere in considerazione a priori per valutare il ritorno di eventuali investimenti. Non parliamo solo della precisone e della tenuta dell’ancoraggio tramite pinze, ganasce, morse meccaniche o pneumatiche. Perché sia realmente valido, un sistema di bloccaggio deve essere: versatile, ovvero compatibile ed adattabile su differenti macchine utensili; espandibile, per poter essere in grado di gestire pezzi di dimensioni e geometrie variabili; modulare, per poter lavorare a diverse altezze.
Per orientarsi nella scelta insomma, occorre prima valutare tutte le possibili applicazioni e situazioni di bloccaggio che il sistema potrebbe trovarsi a dover gestire. Posizionato all’interno di fresatrici e torni CNC, il punto zero è il perno attorno al quale si muovono e lavorano gli utensili della macchina. Più si ambisce a lavorazioni speciali con fori, tasche, scanalature, profili irregolari, maggiore è l’esigenza di un’utensileria ben assortita.
A seconda delle lavorazioni da effettuare, sono necessari differenti tipi di fresa – elicoidali, a denti sfalsati, ad angolo doppio, piane, a candela, a smussare, frontali – e di utensili da tornitura – sgrossatori, finitori, troncatori o filettatori. Per le forature, a seconda del diametro e della finitura del foro, sono necessarie punte con geometrie particolari – integrali, a inserti, a custode, a cannone – possibilmente dotate a loro volta di fori interni per l’adduzione dei lubrorefrigeranti. Con l’obiettivo di soddisfare anche le richieste più particolari, PiacenzaMeccanica porta avanti da anni una politica strutturata di investimenti per abbattere i tempi di produzione e migliorare la qualità dei propri prodotti; non solo attraverso macchinari all’avanguardia, ma anche implementando la propria collezione di utensili.